Ensuring effective sealing of cryogenic liquids can be challenging due to their unique properties and characteristics. The movement of molecules in materials slows as temperatures reduce. And very cold temperatures actually change material physical properties. For example, at 0°C (32°F) water undergoes a phase transition from a liquid to a solid. But once you get even colder starting at -150°C (-238°F), the realm of cryogenics is entered. At -273°C (-459°F), the movement of molecules cease altogether. This is known as “absolute zero” and, in fact, the Kelvin temperature scale was created with this in mind.
In this post, you’ll learn about the design and material considerations crucial to successful sealing of liquids and gases in this extreme temperature range.
Why Cryogenic Temperatures are Useful
Cryogenic temperatures are particularly useful for the phase transition of gases to liquids. Converting a gas to a liquid saves an exceptional amount of space. Liquefaction also reduces transportation expenses and decreases potential hazards that might arise with fluid in a gaseous state.
The table below provides examples of common gases, their boiling points, and liquid-to-gas expansion ratios.
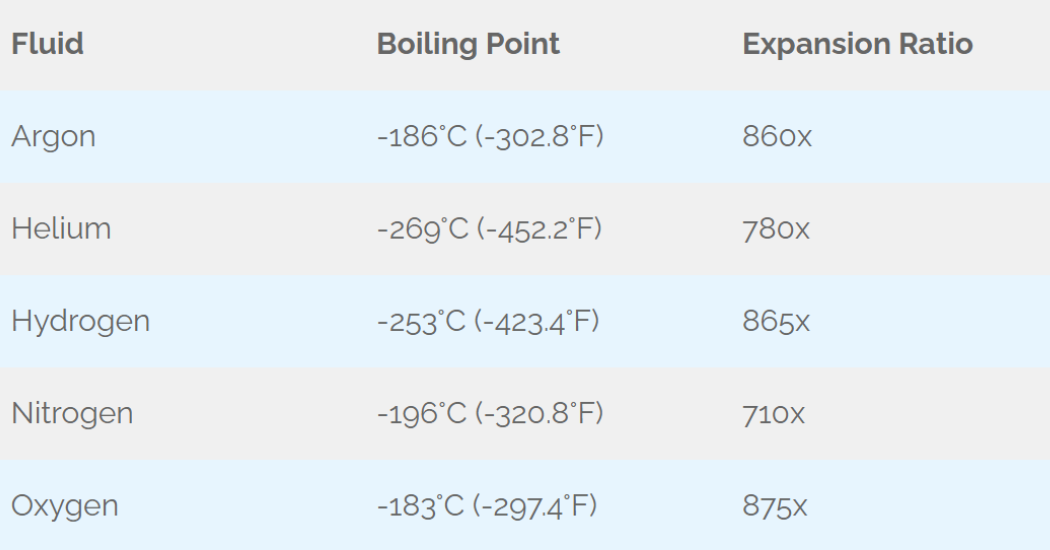
Table 1: Expansion Ratios
Applications for Cryogenic Liquids
Cryogenic liquids have a number of useful applications. Nitrogen is sprayed on harvested produce to cool and delay the ripening process. Cryogenic fuels such as oxygen are used in spacecraft rocket applications. Embryos for in vitro fertilization (IVF) are stored in liquid nitrogen.
But one of the largest industries is around liquefied natural gas (LNG). LNG is used in fleet vehicles as a cleaner burning alternative to gasoline and diesel. LNG can be re-gasified for use in traditional ways such as heating buildings and powering household appliances- cooktops, water heaters, and clothes dryers. It is also becoming a dominant fuel source in the industrial sector for processing things like chemicals, metal, and paper. It is increasingly leveraged in the generation of electricity as a cleaner and less hazardous alternative to coal and nuclear.
Effective Sealing & Safety
Equipment used in the liquefaction, transportation, and storage of cryogenic liquids include pumps, vessels, and valves. These devices are specially designed for cold temperatures. Sealing is extremely important since hazards involved with failure can be life threatening — fire, explosion, frostbite, and asphyxiation.
Traditional compression seals are incapable of cryogenic temperatures. Rubber materials harden, lose flexibility, and resist deformation — all of which can lead to seal failure. So other seal types must be used that can survive application in cryogenic liquids.
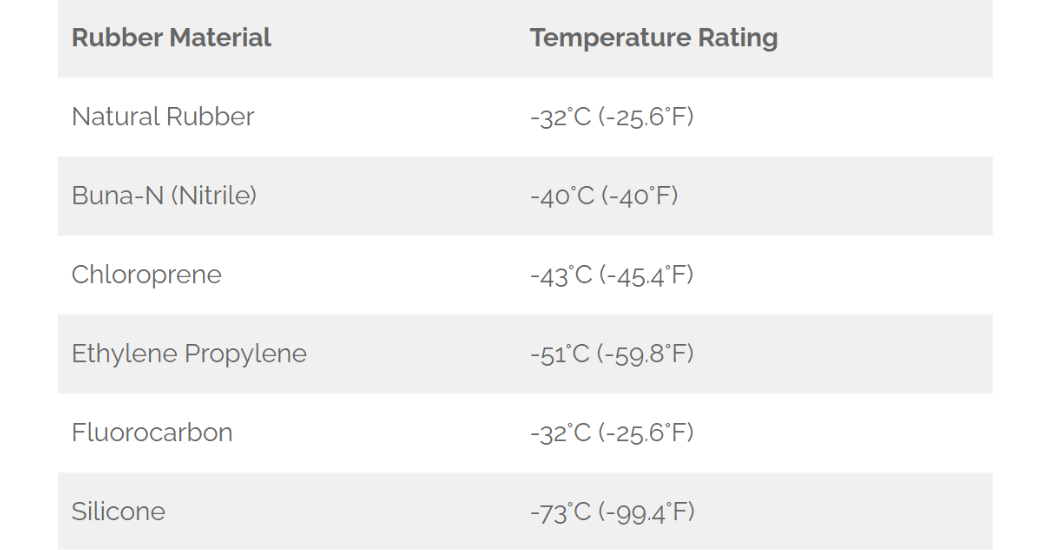
Table 2: Minimum Temperature Rating for Common Elastomers
The Unique Properties of Spring Energized Seals
A spring energized seal (SES) can hold up under the tough conditions imposed by cryogenic liquids.
A spring energized seal consists of a machined polymeric jacket loaded with a spring element. The jacket is typically made from polytetrafluoroethylene (PTFE). This material retains toughness, strength, and lubricity in temperatures down to -268°C (-450°F).
The spring acts to energize the seal lips keeping them in contact with the gland. This provides sealing at low pressure, with subsequent system pressure further actuating the seal.
Seal Design Considerations
There are several design considerations for spring energized seals used in cryogenic service:
- As with all material, cryogenic temperatures harden polymers thereby causing them to become less pliable. Jacket seal lips may be made thinner and longer to remain relatively flexible.
- Also, virgin PTFE rather than filled grades is typically selected in order to minimize impact to pliability. Modified PTFE (TFM) and polychlorotrifluoroethylene (PCTFE) are other base material options that might be used based on the cryogenic application.
- Since the jacket stiffens and temperature drops, high spring loads must be used to overcome the increased material modulus. Single or double flat ribbon coil springs may be used for radial or face seal applications. If the cross-section and diameter are sufficiently large, continuous contact springs may be applied to face seal applications.
- At cryogenic temperatures the coefficient of friction for PTFE and other polymers is reduced. For this reason, seal surfaces are polished to enhance the finish. Further, glands should maintain careful finishes to minimize friction while also helping to ensure gas tight sealing. Recommendations are 2-8 µ-inch Ra for dynamic surfaces and 8-12 µ-inch Ra for static surfaces.
- Finally, the coefficient of thermal expansion (CTE) of polymers is relatively high when compared to metal. This can present a design challenge where the spring energized seal must be carefully fit to the device in which it is installed across the complete temperature range.
- Series 300- Helical Coil Spring Energized Seal
- Series 600- Continuous Contact Spring Energized Seal
Summary
Sealing in cryogenic liquids requires careful design considerations. Materials must be wisely selected, finishes well machined, and fits carefully observed. All of this in order to ensure the media is sealed across a wide temperature spectrum.
If you have any questions about spring energized seals in cryogenic applications, contact your local Chesterton office or “Ask the Expert” service.
For related information, read:
Understanding Spring Energized Seals and When to Use Them
For more information on how to choose spring designs and materials for specific applications, download the Chesterton Spring Energized Seal Guide. Learn more.
About the author: Ron Taylor is the Business Development Manager for the spring energized seal (SES) product line. He has an Engineering background in the design & development of seals and related materials. He is able to promote these through his understanding of markets including Oil & Gas, Aerospace, and Industrial.