If one of your pumps needs an overhaul, it’s time to think about how to maximize its return on maintenance expenses and long-term potential.
Typical mechanical rebuilds for pumps involve impeller truing or replacement, replacement of wear rings and occasional wear ring seats, replacement of bearings, fittings, shaft/sleeve, and packing or mechanical seal installation.
An often-overlooked maintenance expense − and one which can provide a return-on-investment (ROI) for years − is to apply protective coatings to prevent loss of pump performance, improve efficiency, and lower operational energy costs. This relatively simple step can significantly extend the life of the pump and avoid hefty replacement costs. It will also pay off in productivity many times over due to increased Mean Time Between Failure (MTBF).
Loss vs. Gains
The performance of a standard centrifugal cold water pump naturally declines over time – often losing as much as 10-15% of its original efficiency, according to an EU SAVE Report. The same report revealed that many pumps lose 10% after only one year of service!
In our experience, coating brand new pumps can yield 1-3% in long-term efficiency gains. Refurbishing and coating existing pumps has resulted in 5-20% increase.
Unprotected Pump Surfaces = Lost Efficiency and Performance
When pumps are operating under industrial process flows with wide-ranging slurry concentrations, pH swings, temperature cycling, and pressure gradients, the hydraulic flow passages become eroded due to corrosion and or abraded due to suspended particles in the flow.
Critical tolerance areas such as suction throats can open up, which reduces NPSH leading to cavitation. Erosion and corrosion can also impact wear ring seats, leading to increased recirculation and temperature within the pump.
Success Story: Japanese Steel Mill
The Challenge
A steel mill in Japan experienced reduced flow in primary cooling tower pumps used to recirculate quench water to the hot mill. Normally they operated four pumps to maintain the 4000 GPM required flow, with one pump as a spare. However, over time the in-service wear caused the four pumps to lose efficiency, so a fifth pump was added simply to maintain nominal flow. This is a risky position for any plant operation.
The Solution
After considering the coasts and lead time to purchase replacements, they elected to try a maintenance overhaul with coatings used to rehabilitate zones of corrosion and erosion loss.

Wet End (before and after coatings)
The mill took the worst pump and refurbished it with new wear rings, bearings, and an internal protective coating. Take a look at the improvements that occurred:
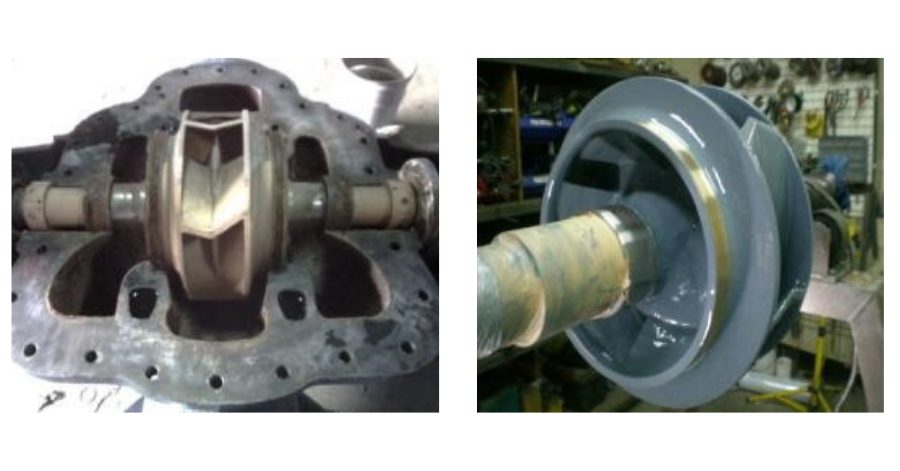
Before and After
The Results
After overhaul the mill noted the following with the treated pump:
- Increased pump performance as measured by flow and discharge pressure
- Reduced the energy consumed for the improved flow generated
- Achieved a more efficient, more reliable, and higher performing pump, which is now protected against future degradation from corrosion and abrasion.
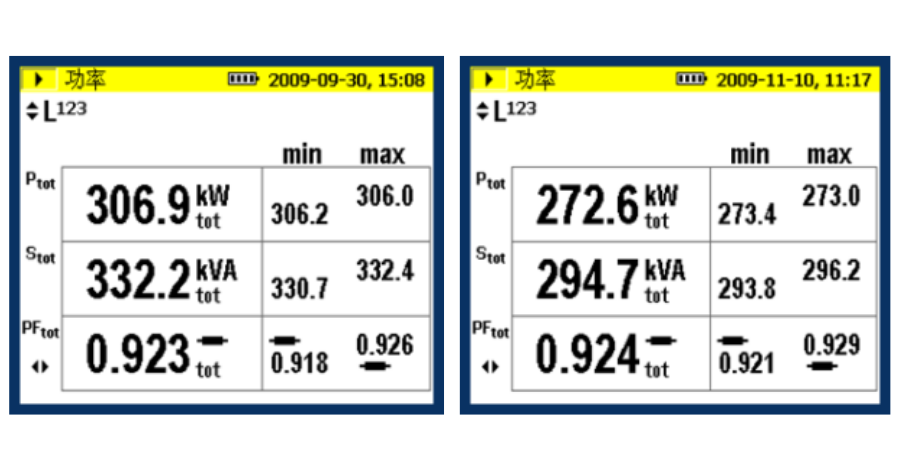
Power Consumption Before and After
The plant was able to rehabilitate all the pumps in the time it took for delivery of one OEM pump. The cost was roughly 37% of the new OEM pumps. When all pumps were rehabilitated, they were able to maintain one pump in the “spare mode.” This netted an electrical energy savings of 1.8 million KWh of energy/year
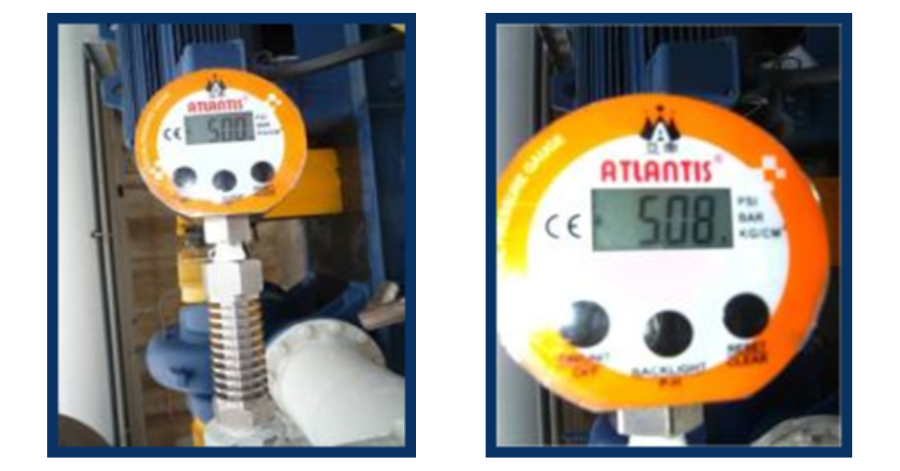
Discharge Pressure Before and After coating
To achieve similar results for your pump operations, contact your local Chesterton office to discuss your pump conditions and the type of refurbishment coatings that will increase performance for the life of the pump.
About the author:
Steve Bowditch is the Global Market Development Manager for ARC Efficiency and Protective Coatings. He is a NACE Level III CIP Inspector and SSPC Corrosion Specialist with over 35 years’ experience in the areas of protective coatings development and applications. When he is not immersed in the exciting world of protective coatings, he is hopefully sailing on a Hinckley Bermuda 40’ somewhere near a tropical island chain.