Problem
Avinashkumar Karre, Principal Process Engineer with Worley, performed a reliability study on a problematic cooling water system (Figure 1).
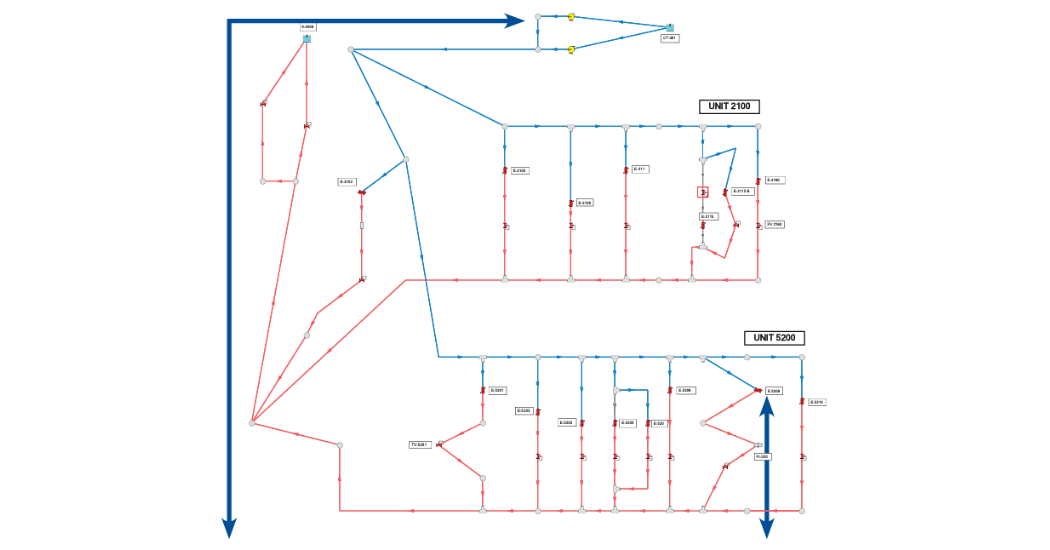
Figure 1: Workspace view of cooling watyer system, balancing flow across 14 consumers.
The system faced a flow imbalance, with some consumers unable to meet duty requirements limiting production. Other consumers received excess flow, resulting in high velocities with accompanying vibration and equipment erosion. The system’s two parallel pumps operated at high flowrates far from the pump’s Best Efficiency Point (BEP) (Figure 1.1).
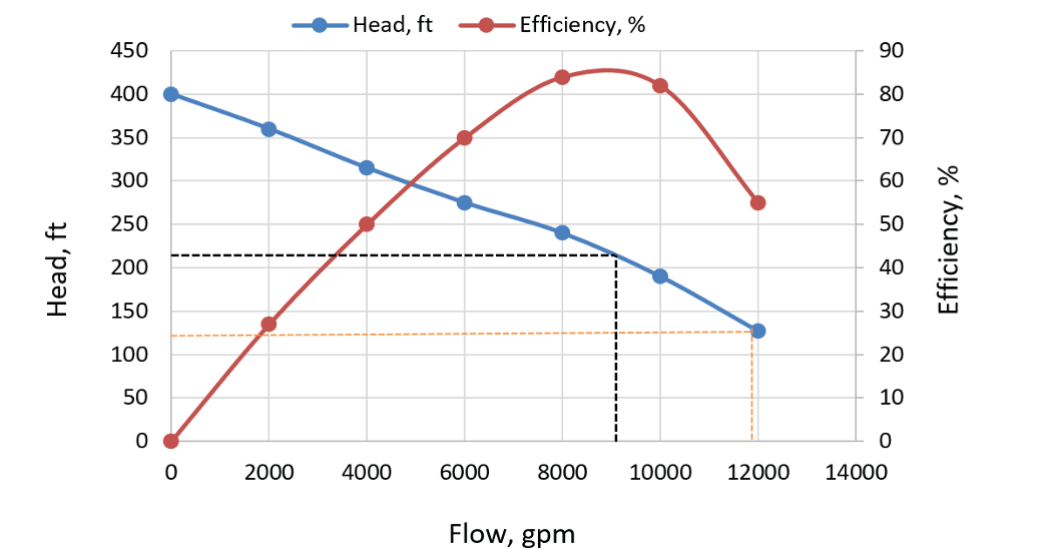
Figure 1.1: Pump efficiency improved from 55% to 84% by reducing flow through the pump
Erosion on piping, tube bundles, and pump impellers required replacement every 4 years, with $2.16M in associated costs and downtime. Addressing the system’s issues had been pending for 15 years, and the project had a challenging schedule due to a short shutdown window.
Analysis
Karre first built and calibrated an AFT Fathom model to within 5% of field measurements. Complex heat exchanger components were modeled based on measured pressure loss data (Figure 1.2).
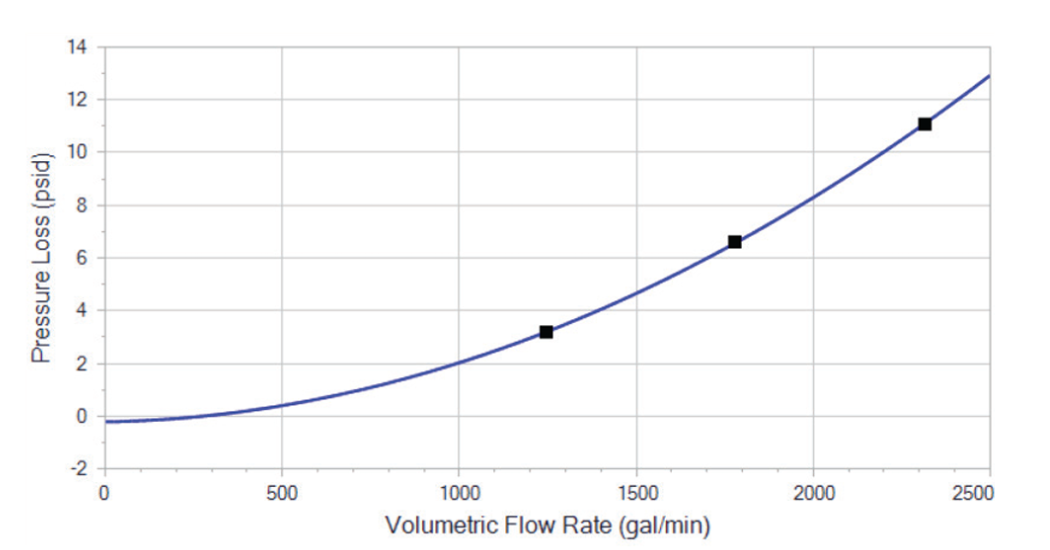
Figure 1.2: Heat Exchanger resistance curve developed from field measured pressure loss data
This ‘base model’ confirmed the poor flow distribution, but also revealed other issues including cavitation and poor control valve operation. Problematic high velocity areas were identified automatically using Design Alerts, ensuring any modified design kept all flow velocities below 12 ft/s (3.6 m/s).
Karre’s ‘modified’ design added restricting orifices and downsized select piping to improve flow balance. Karre could easily compare the ‘base’ and ‘modified’ model results, which also enabled an overall cost analysis for the proposed improvements.
Solution
The additional pressure loss from the recommended layout improved pump operation, increasing efficiency from 55% to 85% (Figure 1.1). The associated energy reduction saved an estimated $287K per year, cost savings which are further improved by fewer impeller replacements.
The proposed design further eliminated operating issues including pipe cavitation and re-sized control valves had improved operating ranges. By addressing the root issues, the client could avoid replacement equipment and associated downtime for repairs.
Karre mentioned the knowledge and approach from this study has been presented at several international industry conferences. The approach now serves as a basis for oil and gas, refining, and chemical projects from different operating companies across US and global projects.