Problem
Protton Synergy assessed pressure surge concerns in a thick paste disposal system. The paste is a by product of a steel manufacturing process with Bingham plastic characteristics. Bingham plastic describes fluids that flow only if a yield stress is exceeded, for example toothpaste or peanut butter.
The fluid’s non-Newtonian characteristic created uncertainty in applying traditional hand calculation approaches to evaluate maximum and minimum pressures during a transient event. The team selected AFT Impulse to accurately model the unique fluid and system across a range of transient events.
Analysis
The paste is piped from a thickener vessel to a series of disposal points via three pumps in series (Figure 1). The basis of the model was imported from a neutral file, using built-in fittings and precise fluid properties to accurately represent the system (Figure 2).
While the client assessed steady-state performance themself using hand calculation spreadsheets, the team confirmed these calculations against their own model results. This comparison reassured the team’s confidence in the tool before proceeding to their transient analysis.
The team was to assess a valve closure, pump trip, and pump trip + restart against ASME B31.3 for maximum pressure and prevent cavitation/vacuum formation as their minimum pressure requirement.
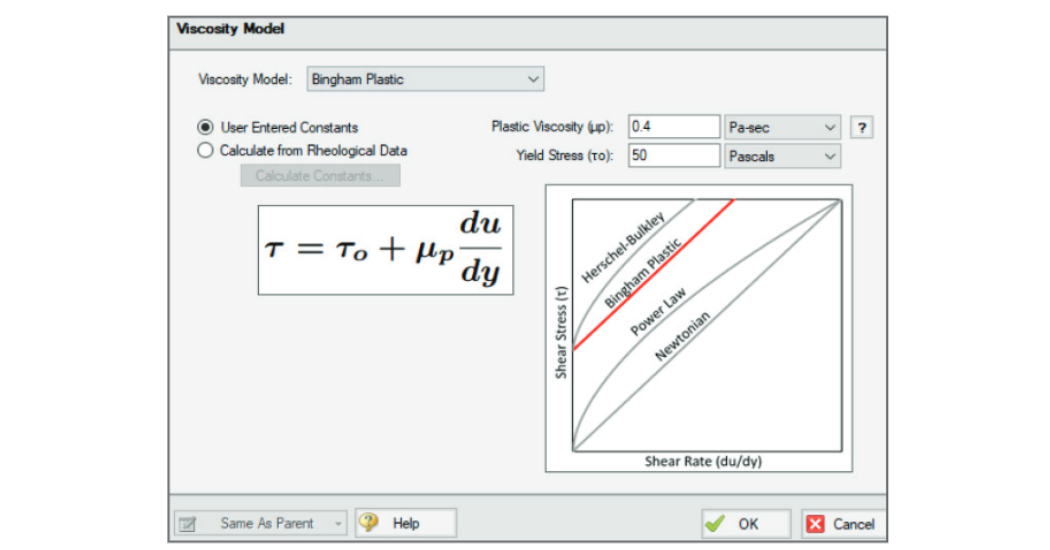
Figure 2: Viscosity model specification for the Bingham plastic paste.
Solution
The initial analysis examined a 10-second valve closure event for maximum and minimum pressure requirements. While the 37 barg (535 psig) peak pressure remained below B31.3’s recommended Maximum Allowable Operating Pressure, the fluid cavitated downstream of the valve where pressure decreased dramatically.
The unacceptable cavitation and other waterhammer concerns were addressed by sizing and locating a series of air valves, relief valves, and check valves. Subsequent valve closure tests with protection equipment in place eliminated cavitation and its accompanying secondary surge when a vapor pocket collapses.
Next the team considered a 15-second simultaneously pump trip of all three series pumps, as well as a pump trip with restart (Figure 3). In both pump cases the peak pressure was 27 barg (390 psig) and the equipment similarly prevented cavitation throughout the system. AFT Impulse was also used to generate unbalanced forces to export for stress analysis, which was used by the Civil Structural team to design support structures.
The team credited AFT Impulse’s flexibility to accommodate changes to layout by the design team and using features like Global Edit to mass update components to avoid input error. Visualization tools to demonstrate results to the client made it easy to communicate the problems and mitigation for the surge analysis, ensuring their system will continue to operate safely.
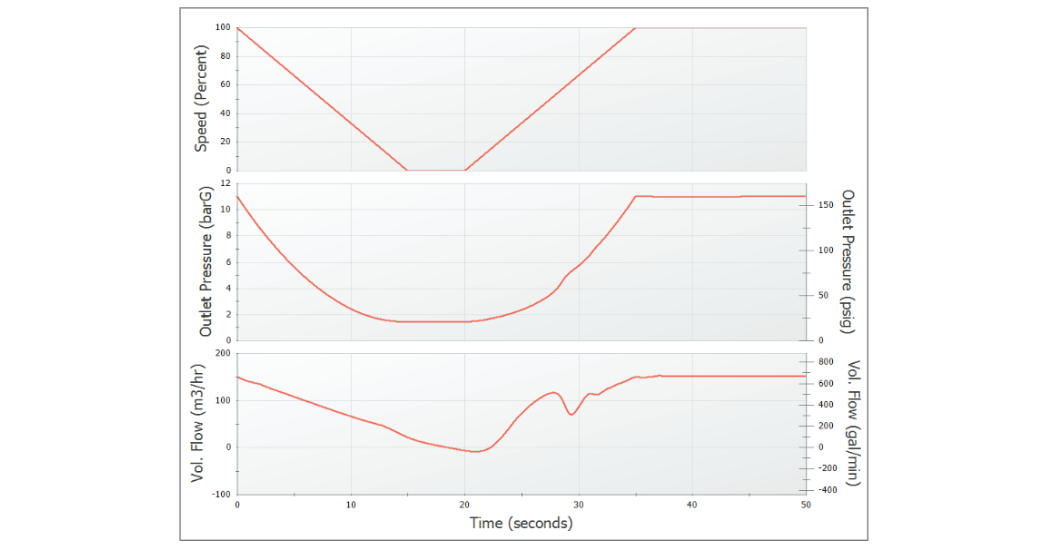
Figure 3: Transient graphs demonstrating how a pump’s speed, outlet pressure, and flowrate varied during the trip + restart event.
Element of Success
The Protton team’s unique non-Newtonian fluid, considerations for both high- and low-pressure concerns, and equipment recommendations that effectively addressed concerns earned the Protton team a Platinum Pipe Award Honorable Mention.
“The detailed Fluid Properties, which is a top-notch feature of AFT Impulse, helps to determine accurate fluid flow behavior for various viscosity models.” – Gaurav Bhende, Kalpesh Birla, and Samarth Pawar