Ross Haimes
Hatch, United Kingdom
Platinum Pipe Award Winner: Most Interesting Model
Ross Haimes, Principal Engineer with Hatch, was tasked with performing a waterhammer analysis on a complex water injection system located offshore in Brazil. The system recycled produced water from the crude refinement process at a Floating Production Storage & Offloading facility (FPSO) to several well head platforms. At the well heads, the produced water was used to reduce the viscosity of heavy crude for transport back to the FPSO for processing, with the remaining water routed to the water injection wells.
The produced water has flow upwards of 140,000 barrels per day to each well head. In 2010, a dynamic study on these subsea flowlines identified waterhammer related issues which were not resolved. The fittings throughout these pipelines also create potential for intermediate reflections, causing concern for interacting pressure waves. The pipelines, ranging in length from 4 to 13 km (2.5 to 8 miles), also had concern for line pack pressure recovery as the flow halted.
Haimes’ analysis began by calibrating a steady-state AFT Impulse model to the physical system (Figure 1). This meant pulling valve loss data, pump curves, material properties, and custom fluid data to adequately model the system. Haimes faced a unique challenge modeling pump automatic recirculation valves, valves which are mechanically linked to the main pump discharge check valve. In essence, the recirculation valve opens when the check valve slams closed and vice-versa to reduce damage to the pump. Other simplifications to the model were made to improve runtime such as combined check valves in pumps and setting a minimum pipe length to improve sectioning.
With the components specified, the model was benchmarked against field data. While not exact, AFT Impulse’s simulated results provided a conservative pressure estimate and was considered sufficient to move forward with transient analysis. Haimes’ analysis focused on 4 cases with potential waterhammer consequences, doing additional sensitivity on flow to each well head in each case as well.
While the peak pressure for each scenario varied, at worst the peak pressure was 312% of the pipe’s current design pressure. The peak pressure often exceeded the Joukowsky predicted pressure rise due to interacting wave fronts and frictional pressure recovery as flow halted. A dead leg pipe in some scenarios helped to dampen the surge effects rather than exacerbate them with reflecting waves.
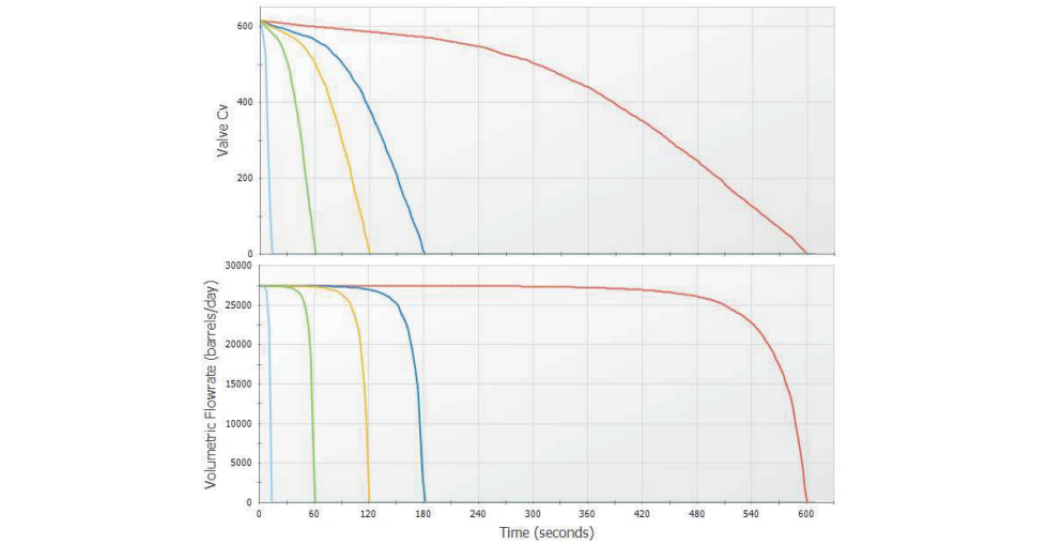
Figure 2: Predicted flowate at the well head valve shows that drastically increasing valve closure time had little impact on slowing flow gradually. The rapid flow reduction led to significant surge in all cases due to the valve’s large initial Cv, which was addressed by closing an upstream valve first.
Haimes’ analysis extended to varying valve closure time to determine a minimum valve closure time. This minimum time was gauged by reducing surge pressure to less than 110% of design pressure. In some cases however, the valve’s initial Cv was so large that it only began controlling flow in the last few seconds of a closure (Figure 2).
This meant the flow was halted incredible quickly at the very end of the valve closure, rendering the closure instantaneous regardless of overall closure time. Even increasing the overall closure time from 6 to 600 seconds made no significant impact on peak pressure experienced after a valve closure. This was due in part to poor surge reduction, but also due to the significant contributions from upstream frictional recovery and additional FPSO pressure (Figure 2). Haimes’ recommendation for this case was to close an upstream valve to avoid these upstream pressure effects.
AFT Impulse provided the flexibility for Haimes to test many potential waterhammer scenarios, considering interacting wave effects and upstream pressure recovery to determine the actual peak pressure for the system. His effective modeling adjustments to significantly improve runtime and his unique valve closure combinations to resolve the surge issue earned him an AFT Platinum PIpe Award for the Most Interesting Model.
Comments