When discussing shaft grounding, it’s typically AC motors that come to mind for most people. But a generator is basically just a motor running in reverse. In a motor, external electric power forces the rotor to spin. In a generator, the input and output are reversed: an external source spins the rotor, producing electric power.
Motors and their coupled equipment are vulnerable to electrical bearing damage. And so are generators and their peripheral equipment. On land, this damage can lead to unplanned downtime and colossal loss of income. But if a sea vessel’s generator or gearbox fails, the ship may be left dead in the water.
This happened to a commercial ship when the auxiliary reduction gears that drove its generator suddenly failed (pictured). Without the gearbox, the 1.5 MW generator couldn’t run, and without the generator, the ship had no electricity. The ship had to return to Shanghai for gearbox repairs. The cause was electrical arcing through the gearbox. Every day’s delay cost the owners $10,000, so they had to get this electrical problem solved, and fast.
They called in Xview Asia, a Hong Kong-based electrical supplier. Xview found that the generator was creating high frequency voltage waves that traveled down the input shaft to the gearbox. There, they discharged to ground by arcing through the gears and bearings. This type of shaft voltage would normally cause circulating currents within the generator, from shaft to frame and back. But the generator’s bearings were insulated. This protected the generator from bearing damage, but left the voltage to seek another path between the shaft and frame. The path it found was through the gearbox to ground.
Insulating the gearbox’s bearings would not solve the problem because the gears would still be vulnerable. But grounding the generator shaft could give the shaft voltage a low-resistance path to ground. Rather than arcing through the gearbox, the voltage would bleed off harmlessly through the grounding device. So Xview tried using carbon brushes to ground the shaft, but they only reduced the maximum voltage from 5.5-6.5 volts to 4.5 (peak to peak). Carbon brushes are good at conducting direct current, but much less good at conducting high frequency alternating current.
So Xview then tried an AEGIS® PRO Shaft Grounding Ring. AEGIS Rings are designed to offer low resistance to high frequency ac electricity. With the PRO Ring installed, shaft voltage was reduced to much lower levels, under 2 volts. Problem solved.
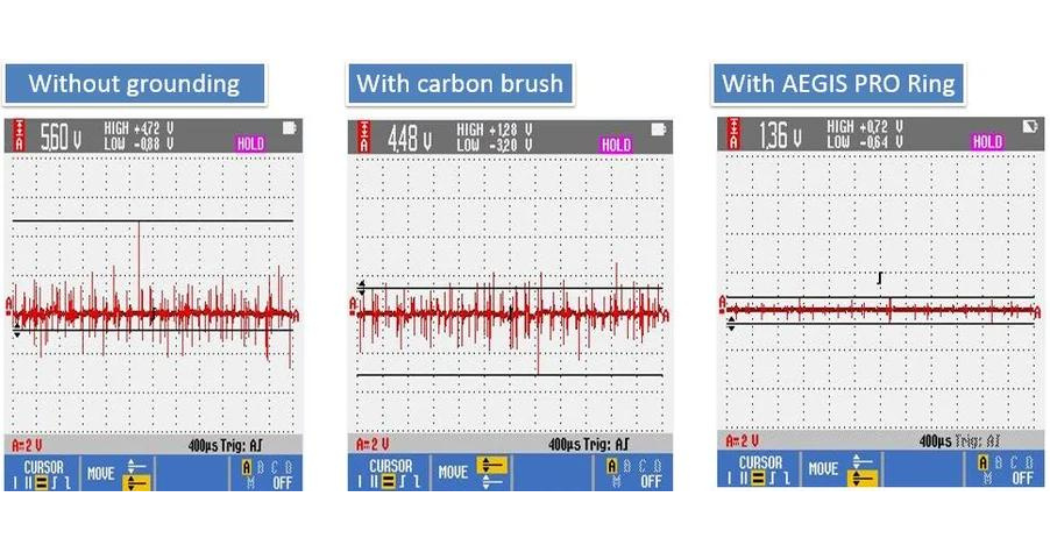
Generator shaft voltage without shaft grounding, with carbon brush, and with AEGIS PRO Ring
The cost to repair the gearbox was over $1 million. The owners were very eager to avoid this kind of damage in the future. Because the PRO solution was so effective, they went on to install PRO Rings on four other ships in their fleet.